Feasibility studies
Feasibility Study to make a decision about investing in a project must have a technical, economic and commercial basis. This study should identify the important factors related to the production of a particular product along with alternative methods for the production of this product and analyze them. Such a study should determine the design with a specific capacity and in a specific location using special technology or technologies that are related to certain materials and inputs, and with specific investment and production costs and sales revenue.
To achieve this goal, we must use the method of sequential testing with a round of information acquisition and comparison with standards and cross-communication. This approach needs to be coordinated with possible alternative solutions for production plans, geographical areas, plant construction sites, mechanical, electrical technology, civil engineering, and organizational structures, in order to minimize production and investment costs.
If the data obtained in this way indicate that the project is unsustainable, the various parameters and production plans, raw materials and technology must be modified in order to present a project that is well described and has durability. . The "feasibility study" should describe this optimization process, justify the assumptions and solutions chosen, and define the scope of the project as a combination of partial and selected alternatives. If the project is not viable despite the alternatives considered, this should be stated and justified in the "feasibility study" (justification plan).
The final estimate of investment and production costs and subsequent calculations of financial and economic viability will only be useful if the scope of the project is explicitly identified in order not to omit the necessary parts and related costs. The scope of the project should be described and determined by maps and tables so that it can be used as an auxiliary structure in the future.
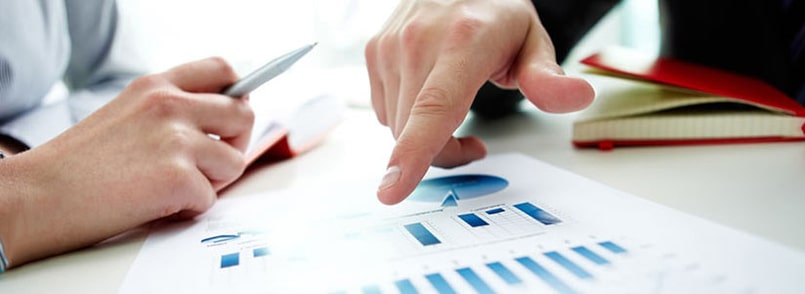
Many "feasibility studies" have the same or similar coverage, although due to factors such as the nature of the industry, the size and complexity of the production unit on the one hand, and investment and other related costs, on the other hand, it may be There are many differences in emphasizing the issues mentioned. But in general, a good "feasibility study" (justification plan) should analyze the main components and consequences of a project, especially since any failure in this area limits the usefulness of the study.
The "feasibility study" must be relevant to existing production factors, the local market and production conditions, and this requires an analysis that must be done in terms of costs and revenues.
The "feasibility study" (justification plan) may be market-based or based on raw materials, meaning that the initiatives used in the "feasibility study" are either derived from existing demand and based on it, or hypothetical. Or is due to the condition of the raw materials.
The "feasibility study" (justification plan) is not an end in itself, but a means to make an investment decision, which should not necessarily agree with the results of the study.
Sections and dimensions of feasibility study
The purpose and nature of a feasibility study were explained according to the issues raised. In the next step, it is necessary to determine what dimensions the feasibility study should have and what sections should be included in its report. First of all, it is necessary to point out the points that should be considered in the feasibility study:
- The process of controlling and building issues
- Identify goals, opportunities and threats
- Description of situations
- Revenue Identification
- Identify costs
- Analyze a project
Stages of feasibility study
The objectives, activities, and items that should be included in a feasibility study were described in the previous sections. In this section, the steps of conducting a feasibility study are explained, which are:
- Step 1: Assess the demand, determine the scope or scope of the project, identify the existing system, identify needs and problems
- Step 2: Review and analyze the goals of the new system, which are usually categorized based on priority and executive priority, so for each goal, stakeholders should be identified.
- Step 3: Identify external entities, note that these entities must be carefully identified and their relationship to the system.
- Step 4: Determine the limiting factors of project implementation, in other words, determine the degree of risk in the success of the project.
- Step 5: Determine the exact scope of the project, identify the needs and reach the customer's approval.
- Step 6: Provide a solution
- Step 7: Economic review of the project, hardware, software, people, place and time costs should be determined.
Having a management team in coordination with the executive team in Saman Samaneh Project-Based Company has caused all projects to be completed with excellent quality and low cost and in accordance with their schedule in the construction and construction stages.